本標準中水容積不大于150L的鋼質焊接氣瓶非等效采用了國際標準ISO 4706:1989《可重復充裝的鋼質焊接氣瓶》。 1 主題內容與適用范圍 本標準規定了鋼質焊接氣瓶(以下簡稱鋼瓶)的基本參數、技術要求、試驗方法、檢驗規則和標志、包裝、運輸、存放等。 本標準適用于在正常環境溫度(-40~60℃)下使用的、水壓試驗壓力不大于7.5MPa(表壓)、公稱容積為10~1000L可重復充裝低壓液化氣體或溶解氣體的鋼瓶。 本標準也適用于重復充裝GB 11174規定的工業用液化石油氣的鋼瓶。 2 引用標準 GB 228 金屬拉伸試驗方法 GB 232 金屬彎曲試驗方法 GB 1804 公差與配合 未注公差尺寸的極限偏差 GB 2106 金屬夏比(V型缺口)沖擊試驗方法 GB 4159 金屬低溫夏比沖擊試驗方法 GB 6397 金屬位伸試驗試樣 GB 7144 氣瓶顏色標記 GB 8335 氣瓶專用螺紋 GB 8337 氣瓶用易熔合金塞 GB 9251 氣瓶水壓試驗方法 GB 11174 液化石油氣 GB 12137 氣瓶氣密性試驗方法 GB/T 13005 氣瓶術語 GB/T 15383 氣瓶水壓爆破試驗方法 JB 4730 壓力容器無損檢測 3 術語、符號 3.1 術語 批量:是指采用同一設計、同一牌號材料、同一焊接工藝、同一熱處理工藝連續生產的鋼瓶所限定的數量。 3.2 符號 a——封頭曲面與樣板間隙,mm; Akv——沖擊吸收功,J; b——焊縫對口錯邊量,mm; c——封頭表面凹凸量,mm; D——鋼瓶公稱直徑,mm; d——彎曲試驗的彎軸直徑,mm; Di——鋼瓶內直徑,mm; Do——鋼瓶外直徑,mm; E——對接焊縫棱角高度,mm; e——鋼瓶筒體同一橫截面最大最小直徑差,mm; h——封頭直邊高度,mm; Hi——封頭內凸面高度,mm; K——封頭形狀系數; L——瓶體長度(包括兩端封頭高度),mm; I——樣板長度,mm; n——彎軸直徑與試樣厚度的比值; P——公稱工作壓力,MPa; Pb——鋼瓶實測爆破壓力,MPa; Ph——水壓試驗壓力,MPa; r——封頭過渡區轉角內半徑,mm; Ri——封頭球面部分內半徑,mm; S——瓶體設計壁厚,mm; S1——筒體設計壁厚,mm; S2——封頭設計壁厚,mm; Sb——瓶體實測最小壁厚,mm; Sk——拉力試樣焊縫寬度,mm; Sh——試樣厚度,mm; Sn——瓶體名義壁厚,mm; V——公稱容積,L; δb——標準規定的抗拉強度,MPa; δba——實測抗拉強度,MPa; δs——屈服應力或常溫下材料屈服點,MPa; △Hi——封頭內高度(Hi+h)公差,mm; δs——短試樣伸長率,%; Ø——焊縫系數; π△Di——內圓周長公差,mm; 4 基本參數 4.1 公稱容積和公稱直徑 鋼瓶公稱容積V和公稱直徑D按表1規定。 表1
公稱容積V L | 10~25 | >25~50 | >50~100 | >100~150 | >150~200 | >200~600 | >600~1000 | 公稱直徑D mm | 200,230 (217) | 250,300 (314) | 300,350 (314) | 400 (350) | 400 (500) | 600 (700) | 800 (900) | 注:()內的數值盡量不采用。 4.2 公稱工作壓力和水壓試驗壓力 鋼瓶公稱工作壓力和水壓試驗壓力按表2規定。 表2 MPa 介質名稱 | 低壓液化氣體 | 溶解乙炔氣體 | 公稱工作壓力P | 5 | 3 | 2 | 1 | | 水壓試驗壓力Ph | 7.5 | 4.5 | 3 | 1.5 | 5.2 | 4.3 許用壓力 鋼瓶許用壓力不得超過水壓試驗壓力的0.8倍。 5 技術要求 5.1 材料一般規定 5.1.1 鋼瓶瓶體材料,必須采用平爐、電爐或吹氧轉爐冶煉的鎮靜鋼,并具有良好的成形和焊接性能。 5.1.2 焊在鋼瓶瓶體上的所有零部件,必須采用與瓶體材料性質相適應的材料。 5.1.3 所采用的焊接材料焊成的焊縫,其抗拉強度不得低于母材抗拉強度規定值的下限。 5.1.4 材料(包括焊接材料)應符合相應技術標準的規定,并必須有質量合格證明書。 5.1.5 鋼瓶制造單位必須對制造鋼瓶主體的材料,按爐罐號進行成品化學成分驗證分析,按批號進行力學性能試驗證試驗。經試驗合格的材料,應做材料標記。 5.2 化學成分 鋼瓶主體材料的化學成分(溶煉分析),應符合表3規定。對含有添加微量合金元素的鋼材,其含量應符合表4規定。 表3 % 化學元素 | C | Si | Mn | P | S | P+S | 不大于 | 0.22 | 0.45(0.60) | 1.60 | 0.04 | 0.04 | 0.07 | 注:()內化學成分的材料適用于制造V>150L的鋼瓶材料。 表4 % 微量合金元素 | Nb | Ti | V | Nb+V | 不大于 | 0.08 | 0.20 | 0.20 | 0.20 | 5.3 力學性能 5.3.1 當鋼瓶瓶體名義壁厚Sn≥6mm時,其主體材料的常溫沖擊吸收功Akv應符合表5的規定。 表5 瓶體名義壁厚Sn,mm | 試樣規格,mm | 試驗溫度,℃ | 沖擊吸收功Akv不大于,J | 6~10 | 5×10×55 | 常 溫 | 15 | -40 | 14 | >10 | 10×10×55 | 常 溫 | 27 | -40 | 20 | 5.3.2 當鋼瓶瓶體名義壁厚Sn≥6mm,且在-20℃以下的環境溫度使用時,若在使用溫度下,按鋼瓶內壓力計算的一次拉伸薄膜應力大于常溫下材料標準屈服點的1/6,則瓶體材料應做-40℃夏比V型缺口沖擊試驗,其沖擊吸收功應符合表5規定。 5.3.3 鋼瓶瓶體材料的屈服比(δs/δb)應不大于0.8。 5.4 設計一般規定 5.4.1 鋼瓶瓶體壁厚計算所依據的內壓力為水壓試驗壓力。 5.4.2 鋼瓶瓶體的組成最多不超過三部分,即縱焊縫不得多于一條,環焊縫不得多于兩條。 5.4.3 鋼封頭的形狀應為橢圓形(見圖1a)、碟形(見圖1b)或半球形,封頭的直邊高度h規定如下: a.當名義壁厚Sn≥8mm時,直邊高度h≥25mm; b.當名義壁厚Sn≥8mm時,直邊高度h≥40mm。 圖1 5.5 瓶體壁厚計算 5.5.1 筒體設計壁厚Si按(1)式計算,并向上圓整,保留一位小數。 Si=PhDi/2δsø/1.3-Ph (1) 式中,焊縫系數Ø規定如下: Ø=1,每條對接焊縫均100%射線透照檢測; Ø=0.9,焊縫射線透照檢測要求按5.13.2條的規定。 5.5.2 封頭設計壁厚S2按(2)式計算,并向上圓整,保留一位小數。 S2=PhDiK/2δs/1.3-Ph (2) 式中,封頭形狀系數K,對標準橢圓封頭(Hi=0.25Di),K=1,其它封頭由圖2查出。 適用于比值Hi/Di在0.20至0.25之間 a 適用于比值Hi/Di在0.25至0.50之間 b 圖2 5.5.3 瓶體設計壁厚S應符合下列規定: a.當鋼瓶內直徑Di<250mm時,不小于2mm; b.當鋼瓶內直徑Di≥250mm時,不小于按(3)式計算的厚度。 S=Do/250+1 (3) 5.5.4 鋼瓶筒體和封頭的名義壁厚應相等,確定瓶體的名義厚度時,應考慮腐蝕裕量、鋼板厚度負偏差和工藝減薄量。 5.6 開孔 5.6.1 不允許在筒體上開孔。在封頭上開孔時,應避開應力集中的部位。 5.6.2 開孔均應考慮補強,補強采用等強度補強方法,補強材料應和瓶體材料相適應,并具有良好的焊接性能。 5.7 焊接接頭 5.7.1 主體焊縫的焊接接頭應采用全焊透對接型式。 5.7.2 縱焊縫不得有永久性墊板。 5.7.3 環焊縫允許采用永久性墊板,或者在接頭的一側做成臺階形的整體式墊板。 5.8 附件 5.8.1 附件的結構設計和布置應便于操作及焊縫的檢查。附件與瓶體的連接時縫應避開瓶體的縱、環焊縫。附件的結構形狀及其與瓶體的連接,應防止造成積液。 5.8.2 底座應保證鋼瓶直立時的穩定性,并具有供排液和通風的孔。 5.8.3 當鋼瓶盛裝介質后的總重量超過40kg時,應考慮吊裝附件或吊裝孔。 5.8.4 選配的瓶閥應滿足所盛裝介質的要求,瓶閥螺紋必須與瓶口螺紋相匹配,并符合有關標準。 5.8.5 鋼瓶應配戴固定式瓶帽或護罩。 5.8.6 鋼瓶及其附件的密封材料,不得與所盛裝的介質發生化學反應。 5.8.7 鋼瓶裝設安全泄放裝置時,其易熔合金不得與瓶內介質發生化學反應,也不得影響充裝質量。 5.8.8 盛裝毒性程度為極度或高度危害介質(如光氣、氟化氫、氯等)的鋼瓶,不得采用泄放裝置。 5.9 組批 鋼瓶制造單位必須根據有關規定按批組織生產。 5.10 焊接工藝評定 5.10.1 鋼瓶制造單位,在生產鋼瓶之前,或需要改變瓶體材料、焊接材料、焊接工藝、焊接設備時,均應進行焊接工藝評定。 5.10.2 焊接工藝評定可以在焊接評定試板上進行,也可以直接在鋼瓶上進行。進行工藝評定的焊縫,應能代表鋼瓶的主要焊縫(縱焊縫、環焊縫)。 5.10.3 焊接工藝評定板應經外觀檢查和100%射線透照檢測,檢測結果應符合5.12條和5.13條的規定。 5.10.4 焊接接頭應進行拉伸、彎曲試驗,當瓶體名義壁厚Sn≥6mm時,還應進行常溫沖擊試驗。當鋼瓶使用符合5.3.2條時,則應改做-40℃低溫沖擊試驗。 5.10.5 焊接工藝評定試驗結果要求如下: a.焊接接頭的抗拉強度應符合5.23條; b.沖擊試驗結果應符合5.3條的表5規定。試驗結果是指三個試樣的算術平均值,允許其中一個試樣比規定的合格數值低1/6; c.彎曲試樣至100°時應無裂紋,試樣邊緣先期開裂可以不計。 5.10.6 焊接工藝評定文件,應經鋼瓶制造單位技術總負責人批準。 5.11 焊接的一般規定 5.11.1 鋼瓶的焊接,必須由按勞動部頒發的《鍋爐壓力容器焊工考試規則》考試合格,并持有效證書的焊工承擔。施焊后,焊工應在所焊之焊縫附近的適當位置打上焊工鋼印,并有可跟蹤的記錄。當有特殊要求時可按圖樣規定。 5.11.2 鋼瓶主體焊縫的焊接,必須采用自動焊接方法,并嚴格遵守經評定合格的焊接工藝。 5.11.3 焊接坡口的形狀和尺寸,應符合圖樣規定。坡口表面清潔、光滑,不得有裂紋、分層和夾雜等缺陷。 5.11.4 焊接(包括焊縫返修)應在室外內進行,室內相對濕度不得大于90%,否則應采取措施。當焊接件的溫度低于0℃時,應在開始施焊的部位預熱。 5.11.5 施焊時,不得在非焊接處引弧。縱焊縫應有引弧板和熄弧板,板長不得小于100mm,去除引、熄弧板時,應采用切除的方法,嚴禁使用敲擊的方法,切除處應磨平。 5.12 焊縫外觀 5.12.1 瓶體對接焊縫的余高為0~3.5mm,同一焊縫最寬最窄處之差不大于4mm。 5.12.2 閥座、塞座角焊縫的幾何形狀應圓滑過渡至母材表面。 5.12.3 瓶體上的焊縫不允許咬邊,焊縫和熱影響區表面不得有裂紋、氣孔、弧坑、凹陷和不規則的突變,焊縫兩側的飛濺物必須清除干凈。 5.13 焊縫射線透照 5.13.1 從事鋼瓶焊縫射線檢測人員,必須按勞動部頒發的《鍋爐壓力容器無損檢測人員資格鑒定考核規則》考試合格,并持有效證書。 5.13.2 采用焊縫系數Ø=1設計的鋼瓶,每只鋼瓶的縱、環焊縫均必須進行100%射線透照檢測。 采用焊縫系數Ø=0.9設計的鋼瓶,對于只有一條環焊縫的按生產順序每50只抽取一只(不足50只時,也應抽取一只)進行焊縫全長的射線透照檢測;對于有一條縱焊縫,兩條環焊縫的鋼瓶,每只鋼瓶的縱、環焊縫均必須進行不少于該焊縫長度的20%的射線透照檢測。 5.13.3 射線透照的部位應包括縱、環焊縫的交接處。 5.13.4 焊縫射線透照檢測按JB 4730進行,射線透照底片質量為AB級,焊縫缺陷等級不低于Ⅱ級。 5.13.5 未經射線透照的瓶體對接焊縫質量也應符合5.13.4條的要求。如經復驗發現僅屬于氣孔超標的缺陷,可由鋼瓶制造單位和用戶協商處理。 5.14 焊縫返修 5.14.1 焊縫返修應按返修工藝進行。返修部位應重新按5.12條及5.13.4條進行外觀和射線透照檢測合格。 5.14.2 焊縫同一部位的返修次數,不應超過兩次。若超過時,每次返修均經技術總負責人批準。 5.14.3 返修次數和返修部位應記入產品生產檢驗記當,并在產品合格證中注明。 5.15 筒體 5.15.1 筒體由鋼板卷焊時,鋼板的軋制方向應與筒體的環向一致。 5.15.2 筒體同一橫截面最大最小直徑差e不大于0.01D。 5.15.3 筒體縱焊縫對口錯邊量b水大于0.1Sn(圖3)。 5.15.4 筒體縱焊縫棱角高度E不大于0.1Sn+2mm(圖4)。用長度1為1/2D但不大于300mm的樣板進行測量。 圖3 圖4 表6 mm 公稱直徑 D | 圓周長公差 π△Di | 最大最小直徑差 e | 表面凹凸量 c | 曲面與樣板間隙 a | 內高代差 △Hi | <400 | ±4 | 2 | 1 | 2 | +5 -3 | 400~700 | ±6 | 3 | 2 | 3 | >700 | ±9 | 4 | 3 | 4 | 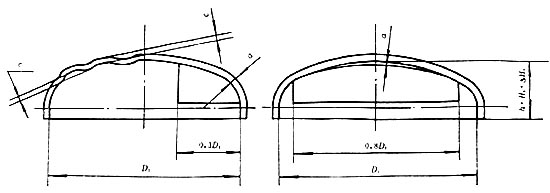 圖5 5.16 封頭 5.16.1 封頭必須用整板鋼板制成。 5.16.2 封頭的形狀與尺寸公差不得超過表6的規定,符號見圖5所示。 5.16.3 封頭實測最小壁厚不得小于封頭設計壁厚與腐蝕裕量之和。 5.16.4 封頭直邊部分的縱向皺折深度不得大于0.25%D,且不得大于1.5mm。 5.17 未注公差尺寸的極限偏差 未注公差尺寸的極限偏差按GB 1804的規定,具體要求如下: a.機械加工件為IT14; b.非機械加工件為IT16; c.長度尺寸為±½IT16。 5.18 組裝 5.18.1 鋼瓶的各零件在組裝前,均應經檢查合格,且不準進行強力組裝。 5.18.2 封頭與筒體對接環焊縫的對口錯邊最b和棱角高度E不得超過表7的規定,檢查尺寸的長度應不小于300mm。 表7 mm 瓶體名義壁厚Sn | 對口錯邊量b | 棱角高度E | <6 | 0.25Sn | 0.10Sn+2 | 6~10 | 0.25>Sn | >10 | 0.10Sn+1 | 5.18.3 當鋼瓶由兩部分組成時,圓柱形筒體部分的直線度應不大于其長度的千分之二。 5.18.4 附件的組裝應符合圖樣的規定。 5.19 表面質量 鋼瓶外表面應光滑,不得有裂紋、重皮、夾雜和深度超過0.5mm的凹坑、劃傷、腐蝕等缺陷,否則應進行修磨,修磨處應圓滑,其壁厚不得小于設計壁厚與腐蝕裕量之和。 5.20 熱處理 鋼瓶在全部焊接完成后,必須進行整體正火或消除應力的熱處理。熱處理應嚴格按熱處理工藝執行。實測記錄應記入產品合格證中。 5.21 容積和重量 5.21.1 鋼瓶的實測水容積應不小于其公稱容積。對于公稱容積大于150L的鋼瓶,其實測容積可用理論容積代替,但不得有負偏差。 5.21.2 鋼瓶制造完畢后應逐只進行凈重的測定。 5.22 水壓試驗和氣密性試驗 5.22.1 鋼瓶水壓試驗應在熱處理后進行。水壓試驗壓力按4.2條確定。在水壓試驗壓力下保壓3~5min進行檢查。鋼瓶不得有宏觀變形、滲漏,壓力表不允許有回降現象。試驗完畢后立即把水放凈,并進行干燥處理。 5.22.2 鋼瓶氣密性試驗必須在水壓試驗合格后進行。低壓液化氣鋼瓶的氣密性試驗壓力為公稱工作壓力,溶解乙炔氣鋼瓶的氣密性試驗壓力為3MPa。在試驗壓力下保壓1~3min,被試驗鋼瓶不得有泄漏現象。 5.22.3 如果在水壓試驗和氣密性中發現焊縫上有泄漏,可按5.14條的規定進行返修。鋼瓶焊縫進行返修后,應重新進行整體熱處理。 圖6 注:X表示焊縫。 圖7 注:X表示焊縫。 5.22.4 焊縫屬下列情況的返修,可不必重新熱處理。 a.針孔泄漏; b.返修長度未超過25mm; c.同一焊縫的返修不多于兩處,且兩處相距不小于75mm。 5.22.5 焊縫返修后,按5.22.1條和5.22.2條的規定,重新進行水壓試驗和氣密性試驗。 5.23 力學性能試驗和爆破試驗 5.23.1 對公稱容積小于或等于150L的鋼瓶,應按批抽取樣瓶進行力學性能試驗和爆破試驗。試驗用鋼瓶必須是經射線透照檢測和逐只檢查合格的鋼瓶。 對公稱容大于150L的鋼瓶,可按批制備產品焊接試板進行力學性能試驗。 5.23.2 在鋼瓶瓶體上進行力學性能試驗時,對于由兩部分組成的鋼瓶,試驗取樣部位按圖6。對于由三部分組成的鋼瓶,試樣取樣部位按圖7。 5.23.3 采用產品焊接試板進行力學性能試驗時,產品焊接試板應和受試鋼瓶在同一塊鋼板(或同一爐批鋼板)上下料,作為受試鋼瓶縱焊縫的延長部分,與縱焊縫一起焊成,并與受試鋼瓶同一爐熱處理。試板應打上受試鋼瓶的瓶號和焊工代號鋼印。試板上的焊縫應進行外觀檢查和100%的射線透照檢測,并符合5.12條和5.13條的規定,焊接試板上,其試樣的取樣位置按圖8。 圖8 1——拉力試樣;2——彎曲試樣;3——沖擊試樣;4——舍棄部分 5.23.4 試樣的焊縫斷面應良好,不得有裂紋、未熔合、未焊透 夾渣和氣孔等缺陷。 5.23.5 力學試驗結果應符合如下規定: a.鋼瓶瓶體母材的實測抗拉強度δba不得大于母材標準規定值的下限,伸長率δ5不小于表8的規定。 表8 瓶體名義壁厚Sn mm | 實測抗拉強度δba | ≤490MPa | >490MPa | δ5,% | <3 | 22 | 15 | ≥3 | 29 | 20 | b.焊接接頭試樣無論斷裂發生在什么位置,其實測抗拉強度δba均不得小于母材標準規定值的下限。 c.焊接接頭試樣彎曲至100°時無裂紋,試樣邊緣的先期開裂可以不計。 d.母材和焊接接頭試樣沖擊試驗結果符合5.3條的規定。試驗結果是指三個式樣的算術平均值,允許其中一個試樣比規定的合格數值低1/6。 5.23.6 鋼瓶爆破試驗結果應符合下列規定: a.在試驗壓力Ph下,鋼瓶的容積殘余變形率不大于10%; b.爆破壓力實測值Pb,不小于按(4)式計算的結果; Pb=2Sb×δb/D0-Sb (4) c.鋼瓶破裂時的容積變形率(鋼瓶容積增加量與試驗前鋼瓶實際容積比)不小于表9的規定: 表9 瓶體長度與公稱直徑比 L/D | δb,MPa | ≤360 | >360~490 | >490 | 容積變形率,% | >1 | 20 | 15 | 12 | ≤1 | 14 | 20 | 8 | d.鋼瓶破裂不產生碎片,爆破口不發生在封頭上(只有一條環焊縫,L≤2D的鋼瓶除外)、縱焊縫及其熔合線上、環焊縫上(垂直于環焊縫除外); e.鋼瓶的爆破口為塑性斷口,即斷口上有明顯的剪切唇,但沒有明顯的金屬缺陷。 5.24 涂漆 5.24.1 鋼瓶經檢查合格,應清除表面油污、銹蝕、氧化皮、焊接飛濺物,并在保持干燥的情況下,方可涂漆。 5.24.2 鋼瓶表面不允許涂膩子。 5.24.3 鋼瓶的顏色標記應符合GB 7144的規定。 6 試驗方法 6.1 材料驗證試驗 鋼瓶材料化學成分和力學性能的驗證試驗,按其材料標準規定的方法取樣分析和試驗。 6.2 焊接工藝評定試板力學性能試驗 6.2.1 按5.10.2條要求,從焊接工藝評定試板(尺寸參照圖8)上截取樣坯時,試樣兩端舍去部分不少于50mm,樣坯一般用機械加工方法截取。采用火焰切割時,必須除去熱影響區。從鋼瓶上用火焰切割截取樣坯時(截取位置參考圖6和圖7),試樣上不得留有熱影響區。 6.2.2 焊接工藝評定用的焊接接頭試樣數量規定如下:拉力試樣2件,橫向彎曲試樣4件(面變、背變各2件),沖擊試樣6件(焊縫、熱影響區各3件)。 6.2.3 試樣上的焊縫的正面和背面,均應進行機械加工,使其與母材齊平,對于不平整的試樣,可以用冷壓法矯平。 6.2.4 拉力試樣按圖9制備,拉伸試驗按GB 228進行。 圖9 6.2.5 彎曲試樣寬度為25mm,彎曲試驗按GB 232進行。試驗時,應使彎軸軸線位于焊縫中心,兩支輥面間的距離應做到試樣恰好不接觸輥子兩側面(見圖10),彎軸直徑d和試樣厚度Sh之間和比值n應符合表10的規定,彎曲角度應符合5.23.5條的規定。 圖10 表10 實測抗拉強度δba MPa | n | ≤430 | 2 | >430~510 | 3 | >510~590 | 4 | >590~685 | 5 | 6.2.6 沖擊試樣的尺寸應符合5.3.1條表5的的規定。焊縫沖擊試樣的缺口軸線應垂直于焊縫表面。熱影響區沖擊試樣的缺口軸線,也應垂直于焊縫表面,且應位于母材熱影響區最嚴重區域。常溫沖擊或低溫沖擊試驗分別按GB 2106和GB 4159進行。 6.3 焊縫射線透照檢測 鋼瓶瓶體縱、環焊縫射線透照檢測按JB 4730進行。膠片放置位置應包括5.13.3條規定的部位,其它部位由射線透照檢測人員或質量檢驗人員確定。 6.4 母材和焊接接頭力學性能試驗 6.4.1 從鋼瓶上截取試樣 6.4.1.1 由兩部分組成的鋼瓶,從圓柱形筒體部分沿縱向截取母材拉力試樣一件,如果筒體部分長度不夠,則從封頭凸形部分切取。從環焊縫處截取焊接接頭的拉力、橫向面彎及背彎試樣各一件(圖6)。 6.4.1.2 由三部分組成的鋼瓶,母材拉力試樣離縱焊縫180°沿縱向從圓柱形筒體部分切取一件,從任一封頭凸型部分截取一件。從縱焊縫處截取拉力、橫向面彎和背彎試樣各一件。如果環焊縫和縱焊縫采用不同的焊接方法(或焊接工藝),則還應從環焊縫處截取同樣數量的試樣(圖7)。 6.4.1.3 當需要從鋼瓶上截取沖擊試樣時,其樣坯可在接近其它試樣規定部位截取。 6.4.2 從產品焊接試板上截取焊接接頭試樣:拉伸試樣2件、橫向面彎和背彎試樣各一件、沖擊試樣(缺口位于焊縫中心)3件。 試板的尺寸和樣坯的截取部位見圖8。 6.4.3 從鋼瓶上或從產品焊接試板上截取樣坯方法,應符合6.2.1條的規定。 6.4.4 焊接接頭試樣的加工應符合6.2.3條的規定。 6.4.5 母材拉力試樣的制備和試驗應分別符合GB 6397和GB 228的規定。 6.4.6 焊接接頭拉力、彎曲和沖擊試樣的制備及其試驗按6.2.4條至6.2.6條的規定進行。 6.5 重量和容積測定 6.5.1 采用稱量法測定鋼瓶的重量和容積。重量單位為千克(kg),容積單位為升(L)。 6.5.2 稱量應使用最大稱量為實際稱量1.5~3.0倍的衡器,其精度應能滿足最小稱量誤差的要求,其周檢期不應超過三個月。 6.5.3 重量和容積測定應保留三位有效數字,其余數字對于重量應進1,對于容積應舍去,示例如下: 實測凈重和容積 1.064 5 10.676 106.55 重量應取為 1.07 10.7 107 容積應取為 1.06 10.6 106 6.6 瓶體壁厚測量 瓶體壁厚使用超聲波測厚儀進行測量。 6.7 水壓試驗 鋼瓶水壓試驗按GB9251的有關規定進行,試壓時應以每秒不大于0.5MPa的升壓速度,緩慢地升至試驗壓力。 6.8 氣密性試驗 鋼瓶氣密性試驗按GB12137的有關規定進行。 6.9 爆破試驗 6.9.1 鋼瓶爆破試驗采用水壓,其方法按GB15385的要求進行,并應遵循下列規定: a.試驗的環境溫度和試驗用水的溫度不應低于5℃; b.試驗系統不得有滲漏,不得存留氣體; c.試驗時必須用兩個量程相同、且量程為試驗壓力2.0~3.0倍,精度不低于1.5級的壓力表,其周檢期不得超過一個月; d.試壓泵每小時的送水量不應超過鋼瓶水容積的5倍; e.試驗時應有可靠的安全措施。 6.9.2 進行爆破試驗前,應先按6.5條測定鋼瓶實際容積。 6.9.3 進行爆破試驗時,先按GB9251的外測法試驗或內測法試驗確定在水壓試驗壓力Ph下的鋼瓶容積變形量和殘余變形率,然后再緩慢升壓,并測量、記錄壓力和時間或進水量的對應關系,繪制相應的曲,確定鋼瓶開始屈服的壓力、升壓直至爆破并確定爆破壓力和總進水量為止,并計算爆破容積變形率。 6.10 外觀檢查 用目測檢查鋼瓶表面、焊縫外觀及其附件。 7 檢驗規則 7.1 材料檢驗 7.1.1 鋼瓶制造單位應按6.1條規定的方法對制造鋼瓶瓶體的材料,按爐罐號進行成品化學成分驗證分析,按批號進行力學性能驗證試驗。成品化學成分驗證分析結果和熔煉化學成分的偏差,應符合該材料標準的規定。 7.1.2 驗證分析試驗結果,應符合5.1.4條和5.2條的規定。當鋼瓶瓶體壁厚等于或大于6mm時,沖擊試驗應符合5.3條的規定。 7.2 逐只檢驗 7.2.1 鋼瓶逐只檢驗應按表11規定的項目進行。 7.2.2 采用焊縫系數Ø=0.9設計的鋼瓶,對于有一條縱焊縫、兩條環焊縫的,每只鋼瓶應進行不少于其縱、環焊縫相應長度總長20%的射線透照檢測,如發現超過標準規定的缺陷,應在該缺陷兩端各延長該焊縫長度20%的射線透照檢測,一端長度不夠時,在另一端補足,若仍有超過標準規定的缺陷時,則該鋼瓶的縱、環焊縫應進行100%的射線透照檢測。 7.3 批量檢驗 7.3.1 分批和抽樣規則 7.3.1.1 對于只有一條環焊縫,并采用焊縫系數Ø=0.9設計的鋼瓶,按生產順序每50只抽取一只(不足50只時應抽取一只)進行焊縫全長的射線透照檢測。 7.3.1.2 對于公稱容積小于或等于150L的鋼瓶,以不多于500只為一批,從每批鋼瓶中抽取力學性能試驗和爆破試驗瓶各一只。 7.3.1.3 對于公稱容積大于150L的鋼瓶,以不多于50只為一批,做一塊產品焊接試板進行力學性能試驗。 7.3.2 檢驗項目 鋼瓶批量檢驗項目按表11規定。 7.3.3 復驗規則 7.3.3.1 在批量檢驗中,如有不合格項目,應進行復驗。 7.3.3.2 批量檢驗項目中,如有證據證明是操作失誤或試驗設備失靈造成試驗失敗,則可在同一鋼瓶(必要時也可在同批鋼瓶中另抽一只)或原產品焊接試板上做第二次試驗。第二次試驗合格,則第一次試驗可以不計。 7.3.3.3 焊縫全長的射線透照檢測不合格時,應在同一生產順序50只中,再抽取二只鋼瓶進行焊縫全長的射線透照檢測,若仍不合格,則應逐只進行焊縫全長的射線透照檢測。 7.3.3.4 公稱容積小于或等于150L的鋼瓶進行的力學性能試驗或爆破試驗不合格時,應按表12的規定進行復驗,復驗鋼瓶在同批中任選。 表11 序號 | 檢 驗 規 則 | 逐只檢驗 | 批量檢驗 | 檢驗方法 | 判定依據 | 1 | 簡 體 | 最大最小直徑差 e | △ | | | 5.15.2 | 2 | 縱焊縫對口錯邊量 b | △ | | 5.15.3 | 5.15.3 | 3 | 縱焊縫棱角高度 E | △ | | 5.15.4 | 5.15.4 | 4 | 直線度 | △ | | | 5.18.3 | 5 | 封 頭 | 內圓周長公差 π△Di | △ | | | 5.16.2 | 6 | 表面凹凸量 c | △ | | 5.16.2 | 7 | 最大最小直徑差 e | △ | | | 8 | 曲面與樣板間隙 a | △ | | 5.16.2 | 9 | 內高公差 △Hi | △ | | | 10 | 直邊部分縱向皺折深度 | △ | | | 5.16.4 | 11 | 環焊縫對口錯邊量 b | △ | | 5.18.2 | 5.18.2 | 12 | 環焊縫棱角高度 E | △ | | 5.18.2 | 5.18.2 | 13 | 鋼瓶表面 | △ | | 6.10 | 5.19 | 14 | 焊縫外觀 | △ | | 6.10 | 5.12 | 15 | 瓶體壁厚 | △ | | 6.6 | 5.16.3、5.19 | 16 | 射線透照 | △ | △ | 6.3 | 5.5.1、5.13.4 | 17 | 力學性能 | | △ | 6.4 | 5.23 | 18 | 重量 | △ | | 6.5 | 5.21.2 | 19 | 容積 | △ | | 6.5 | 5.21.1 | 20 | 水壓試驗 | △ | | 6.7 | 5.22.1 | 21 | 氣密性試驗 | △ | | 6.8 | 5.22.2 | 22 | 爆破試驗 | | △ | 6.9 | 5.23.6 | 23 | 附件 | △ | | 6.10 | 5.8 | 表12 只 批 量 | 不合格項目 | 復驗項目 | ≤250 | 1M | 2M 1B | 1B | 1M 2B | >250~500 | 1M | 2M 2B | 1B | 1M 4B | 注:M——力學性能試驗; B——爆破試驗。 7.3.3.5 按7.3.3.4條復驗仍有一只以上鋼瓶不合格時,則該批鋼瓶為不合格。但允許對這批鋼瓶進行修理,清除缺陷后再重新熱處理,并按7.3條的規定,作為新的一批重新檢驗。 7.3.3.6 公稱容積大于150L的鋼瓶,其產品焊接試板力學性能試驗如有不合格的項目,經加倍復驗仍不合格時,允許從該批鋼瓶中任選一只,按6.4.1.2條的規定截取試樣重做試驗,如還有不合格的項目,則這批鋼瓶為不合格。但允許重新熱處理,按6.4.1.2條規定做為新的一批重新檢驗。 8 標志、包裝、運輸、存放 8.1 鋼瓶上的鋼印標志的內容、位置和要求,應符合勞動部頒發的《氣瓶安全監察規程》和鋼瓶設計圖樣的規定。鋼印標志中瓶體設計壁厚,應標志簡體或封頭設計壁厚兩者中較厚的壁厚。 8.2 出廠鋼瓶的包裝,應根據與用戶簽訂的協議中關于包裝的要求進行,如用戶無要求時,則按制造單位的技術規定進行。 8.3 鋼瓶在運輸和裝卸過程中,要防止碰撞、劃傷和損壞附件。 8.4 鋼瓶應存放在沒有腐蝕氣體,并通風、干燥、不受日光曝曬的地方。 9 出廠文件 9.1 出廠的每只鋼瓶,均應附有產品合格證,產品合格證所記入的內容應和制造單位保存的生產檢驗記錄相符,產品合格證的格式和內容見附錄A(參考件)。 9.2 出廠的每批鋼瓶,均應附有批量檢驗質量證明書。該批鋼瓶有一個以上用戶時,可提供批量檢驗質量證明書的復印件給用戶,批量檢驗質量證明書的格式和內容見附錄B(參考件)。 9.3 制造單位應妥善保存鋼瓶的檢驗記錄和批量檢驗質量證明書的復印件(或正本),保存時間應不少于7年。 附 錄 A 產 品 合 格 證 (參考件) xxxxx廠 鋼質焊接氣瓶 產 品 合 格 證 鋼瓶名稱_______________________________________________ 產品編號_______________________________________________ 鋼瓶批號_______________________________________________ 出廠日期_______________________________________________ 制造許可證_____________________________________________ 本產品的制造符合GB 5100-94《鋼質焊接氣瓶》和設計圖樣要求。經檢驗合格。 檢驗科長(章) 質量檢驗專用章 年 月 主要技術數據: 公稱容積 L 實際容積 L 內直徑 mm 總長度 mm 充裝介質 最大充裝量 kg 筒體設計壁厚 mm 封頭設計壁厚 mm 筒體、封頭鋼板牌號 材料標準代號 材料化學成分規定值,%: C Si Mn P S P+S 材料強度規定值:δb MPa δs MPa 鋼瓶凈重(不包括可拆件) kg 熱處理方式 加熱溫度 ℃ 保溫時間 h 冷卻方式 水壓試驗壓力 MPa 氣密性試驗壓力 MPa 焊縫系數Ø 焊縫射線透照檢測 依據標準 檢測比例 合格級別 檢測結果 焊縫返修次數 1次__________處, 2次__________處, 3次__________處。 焊縫返修部位展開簡圖。 (三部分組成) (兩部分組成) 使用說明: 內容由制造單位編寫,但必須有遵守勞動部有關規程,最高使用溫度以及使用注意事項等方面的條款。 鋼瓶簡圖: | 注:規格要統一,表心尺寸推薦150mm×100mm。 附 錄 B 批量檢驗質量證明書 (參考件) xxxx廠 鋼質焊接氣瓶批量檢驗質量證明書 鋼瓶名稱___________________________________________________ 盛裝介質及化學分子式_______________________________________ 圖號_______________________________________________________ 出廠批號___________________________________________________ 出廠日期___________________________________________________ 制造許可證編號_____________________________________________ 本批鋼瓶共 只,編號從 號到 號,經檢查和試驗符合 GB 5100-94的要求,是合格產品。 安全監察機關檢查專用章 制造廠檢驗專用章 監察員 檢驗科長 年 月 日 年 月 日 制造廠地址: 郵政編碼 1 主要技術數據 公稱容積 L 公稱工作壓力 MPa 公稱直徑 mm 水壓試驗壓力 MPa 瓶體名義壁厚 mm 氣密性試驗壓力 MPa 2 試驗瓶的測量 (V>150L時,指帶試板的瓶) 試驗 瓶號 | 實際容積 L | 凈 重 kg | 最小實測壁厚,mm | 熱處理爐號 | 筒體 | 封頭 | | | | | | | 注:凈重不包括可拆件。 3 瓶體材料化學成分 % 4 焊接材料 5 鋼瓶及試板熱處理 方法 加熱溫度 ℃ 保溫時間 h 冷卻方式 6 焊縫射線透照檢測 焊縫總長 mm 檢查比例 % 按JB 4730檢測 級合格 試驗用瓶(V>150L時,指帶試板的瓶) 返修1次 處,返修2次 處,返修3次 處。 7 力學性能試驗 試板編號 | 抗拉強度 δb MPa | 伸長率 δ5 % | 彎曲試驗 | 沖擊值,J | 橫向 面彎 | 橫向 背彎 | V型缺口 常溫 | V型缺口 -40℃ | | | | | | | | | | | | | | | 試樣數量 | 2 | 2 | 1 | 1 | 3 | 3 | 8 水壓爆破試驗(V≤150L) 試驗瓶號 | 爆破壓力 MPa | 開始屈服壓力 MPa | 試驗壓力下容積殘余變形率 % | 爆破時容積變形率 % | | | | | | | | | | | | | | | | 9 試驗用瓶(公稱容積V>150L時,指帶試板的瓶) 返修部位(簡圖) 10 試驗瓶(V≤150L)爆破位置和形狀簡圖 質量檢驗員專用章 | 注:規格要統一,表心尺寸推薦為150mm×100mm。 附加說明: 本標準由中華人民共和國勞動部提出。 本標準由全國氣瓶標準化技術委員會歸口。 本標準由北京金屬結構廠、石家莊化工機械廠、常州飛機制造廠、上海化工機械一廠負責起草。 本標準主要起草人林志民、陳士光、侍靜遠、張而立。 |